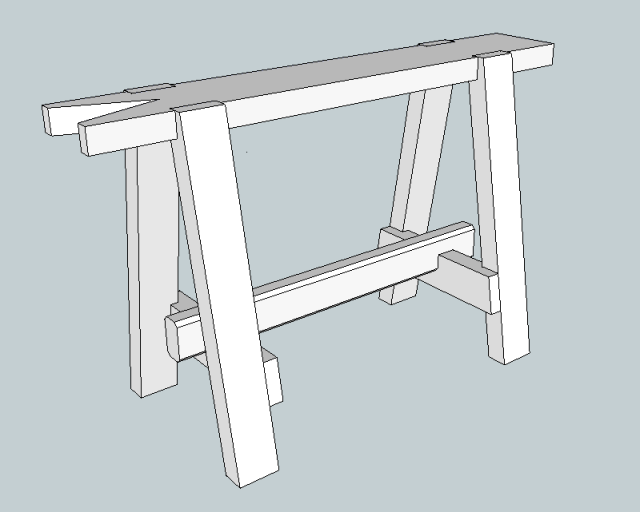
While working through the Stickley Lost Side Table project, I realized that my current saw bench, a basic five-board bench, was less than ideal for ripping stock. It’s a bit too wide, so when I get a narrow piece out over the edge, the bench is quite tippy.
Chris Schwarz has been teaching a two-day class on building a traditional English saw bench for a while; a few years ago a DVD was produced following the class. I like the design of this bench; it’s has a narrower top, which means you don’t have to stretch as far when ripping. Plus, it’s fairly straightforward to build from basic construction lumber. I picked up a couple 16′ 2×12’s from the local lumber yard and set them aside to dry. I used 2×12’s because they tend to be clearer (free of knots) than shorter, narrower lengths and you can usually get some decent quarter sawn material out of the edges.
I started out ripping the boards I needed from the 2x12s, leaving a bit of room for planing and shooting to length. The top board is about 5″ wide by 32″ long, roughly a hand width by half my height. The bench will end up being 19″ tall, the height from the floor to the bottom of my kneecap. The legs were all ripped out, shooting for 2.5″ wide, but they all vary. They all vary in absolute thickness as well, one of the consequences of working by hand.
After I sawed the boards to rough size, I 3-squared each of the legs (face + two long edges) and then squared up (shot) one end. From there, I marked out the little bird’s mouth that fits into a gain in the top board.
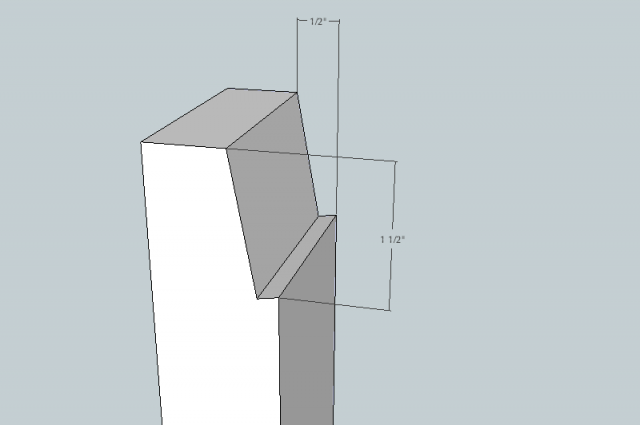
Cutting the bird’s mouth is just like cutting a tenon. Saw across the top, then down each side to establish a kerf. Then just follow the kerfs all the way to the bottom.
To clean up the joint, I deviated from Chris’s method (disobey me?). I found that lining up the knife lines against a wooden parallel clamp to be too fiddly. There’s a fair bit of slop in the cams on my set of clamps, so the two wooden pieces wouldn’t stay in plane. I just attacked it with a wide chisel and a shoulder plane, working to the knife lines. I also didn’t gang up the legs and plane them like they show in the video; my legs were all different thicknesses and the out face is not a true face, so it would have just thrown all my shoulder plane work out the window.
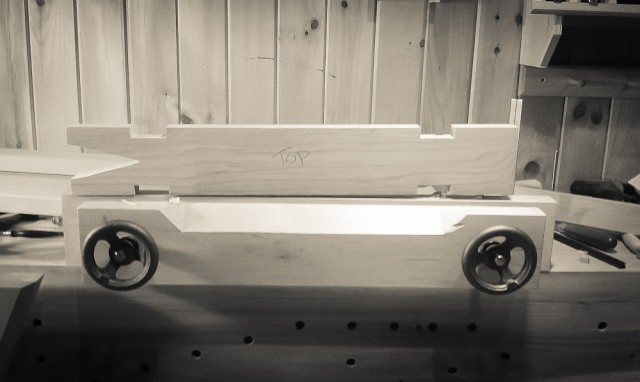
The gains were easy to layout and cut. I made a mark 4.5″ inches from each end, then laid each leg against the mark and used that to layout the far side of the gain. I sunk them 3/4″ into the leg, using a cutting gauge to lay out the baseline and a square to mark the edges. Saw down, then pop out most of the waste with a chisel, being careful to watch how the grain runs. It’s very easy to take too big a bite and have the grain run out way below your marked line, especially in this hem/fir/wtf that I used.
Glue, clamps and an overnight wait and the legs were on.
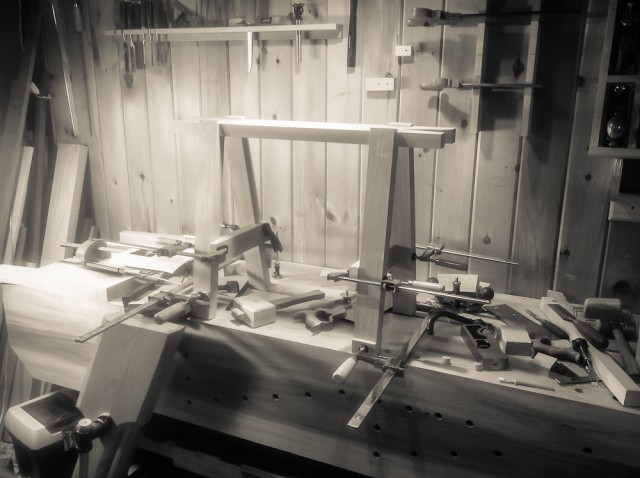
This morning I pulled the clamps and started work on the short braces. I used a 12″ ruler as a stop block to mark a spot on the inside of each leg, then clamped the short braces in place, making sure the two braces were coplanar by sighting over them from a distance, much like using winding sticks.
I marked the shoulder line right from the piece, then pulled it all back apart. Some more sawing (1/2″ fillister this time) and cleanup with a router plane and the braces were done. Back into clamps and glue for another day long bake.
Hopefully tomorrow I can add the long stretcher that connects the braces, add some nails and finish it off.